Types of Inventory
Inventory refers to the stock of goods and materials that a business holds for the purpose of resale, production, or consumption. Effective inventory management is essential for maintaining the right balance between supply and demand, reducing carrying costs, and preventing stockouts or overstock situations. Businesses across various industries, including retail, manufacturing, and service sectors, manage different types of inventory to meet their specific operational requirements.
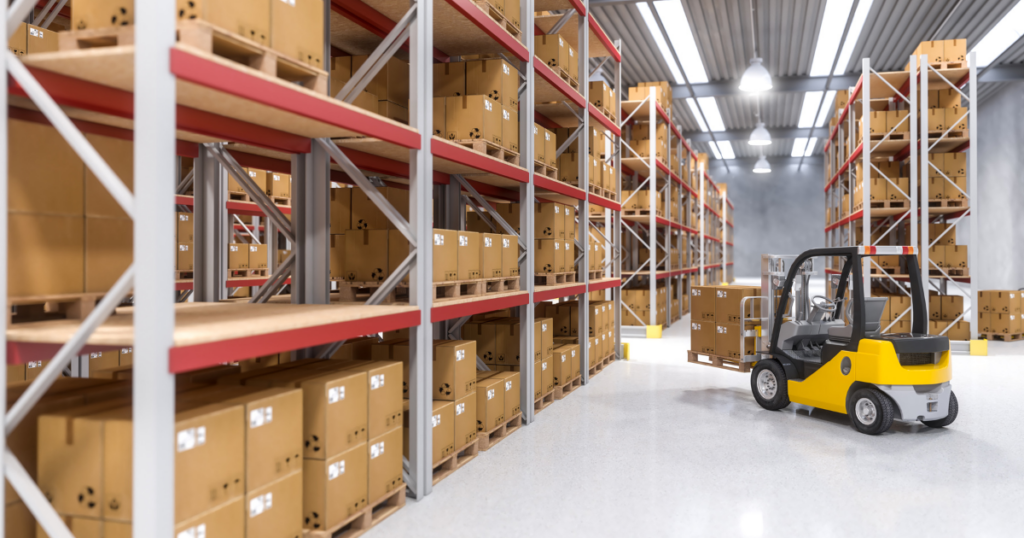
15 Types of Inventory
1. Raw Materials Inventory:
Raw materials inventory consists of the basic components or materials that are used in the production process. These materials are typically purchased from suppliers and are transformed into finished goods through manufacturing processes. Examples of raw materials include wood, steel, plastic, fabric, and chemicals.
2. Work-in-Progress (WIP) Inventory:
Work-in-progress inventory represents partially completed products that are still undergoing production but have not yet reached the finished goods stage. This type of inventory includes items that are being assembled, processed, or manufactured. WIP inventory is an important measure to track production efficiency and identify bottlenecks in the manufacturing process.
3. Finished Goods Inventory:
Finished goods inventory refers to the final products that are ready for sale or distribution to customers. These items have completed all manufacturing processes and are packaged and labeled appropriately. Examples of finished goods include electronics, clothing, furniture, and food products.
4. Maintenance, Repair, and Operations (MRO) Inventory:
MRO inventory consists of supplies and materials that are necessary for the maintenance, repair, and operations of a business. These items are not directly used in the production process but are essential for keeping the business running smoothly. MRO inventory can include items such as tools, spare parts, lubricants, cleaning supplies, and safety equipment.
5. Pipeline Inventory:
Pipeline inventory refers to goods that are in transit between different locations within the supply chain. This can include items being transported from suppliers to manufacturers, from manufacturers to distributors, or from distributors to retailers. Pipeline inventory is important to consider when calculating lead times and ensuring a smooth flow of goods throughout the supply chain.
6. Anticipation Inventory:
Anticipation inventory is stock that is held in anticipation of an expected increase in demand or a potential shortage of supply. This type of inventory is often used to mitigate the risk of stockouts or delays in production. Anticipation inventory can be built up in preparation for seasonal demand fluctuations, promotional campaigns, or anticipated disruptions in the supply chain.
7. Cycle Inventory:
Cycle inventory refers to the amount of stock that varies with the production cycle or order quantity. It is the result of ordering and producing in batches rather than continuously. Cycle inventory is influenced by factors such as order frequency, production setup time, and economic order quantity (EOQ) calculations. By optimizing cycle inventory, businesses can reduce carrying costs and improve efficiency.
8. Decoupling Inventory:
Decoupling inventory is used to separate different stages of the production process and buffer against variations in supply and demand. It acts as a buffer between different workstations or processes, allowing them to operate independently without causing disruptions. Decoupling inventory helps to prevent bottlenecks and maintain a smooth flow of production.
9. Transit Inventory:
Transit inventory refers to goods that are in transit between different locations but have not yet reached their final destination. This can include items being transported by trucks, ships, trains, or airplanes. Transit inventory is important to consider when calculating lead times and ensuring timely delivery to customers.
10. Deadstock Inventory:
Deadstock inventory consists of items that are no longer in demand or have become obsolete. These products are unlikely to be sold and may take up valuable storage space. Deadstock inventory can result from poor forecasting, changes in customer preferences, or technological advancements that render certain products obsolete.
11. Consignment Inventory:
Consignment inventory is stock that is held by a retailer but still owned by the supplier or manufacturer. The retailer only pays for the inventory once it is sold to the end customer. This arrangement allows suppliers to have their products displayed in retail stores without taking on the risk of unsold inventory.
12. Safety Stock Inventory:
Safety stock inventory is a buffer stock that is held to protect against unexpected fluctuations in demand or supply. It acts as a safety net to prevent stockouts and ensure that customer orders can be fulfilled even during unforeseen circumstances such as supplier delays or sudden spikes in demand.
13. Seasonal Inventory:
Seasonal inventory refers to goods that are specifically stocked to meet the increased demand during certain seasons or holidays. This type of inventory is common in industries such as retail, fashion, and food where demand fluctuates significantly throughout the year. By stocking up on seasonal inventory, businesses can take advantage of peak sales periods and maximize revenue.
14. Conserved Inventory:
Conserved inventory is stock that is intentionally held back or conserved for future use. This can include spare parts, components, or materials that are not immediately needed but may be required for repairs, replacements, or future production runs. Conserved inventory helps to ensure business continuity and minimize downtime.
15. Obsolete Inventory:
Obsolete inventory consists of items that are no longer usable or saleable due to various reasons such as expiration, damage, or changes in technology. This type of inventory should be disposed of or liquidated to free up storage space and prevent further losses.
In conclusion, understanding the different types of inventory is crucial for effective inventory management and optimizing business operations. From raw materials and work-in-progress to finished goods and obsolete items, each type of inventory plays a specific role in the supply chain. By carefully managing and controlling these inventories, businesses can improve efficiency, reduce costs, and meet customer demands more effectively.