Effective Returns Management in Warehouse Operations
Returns management is a critical aspect of warehouse operations that can significantly impact a company’s profitability and customer satisfaction. With the rise of e-commerce and online shopping, the volume of returns has increased, making it essential for businesses to have an efficient and effective returns management process in place.
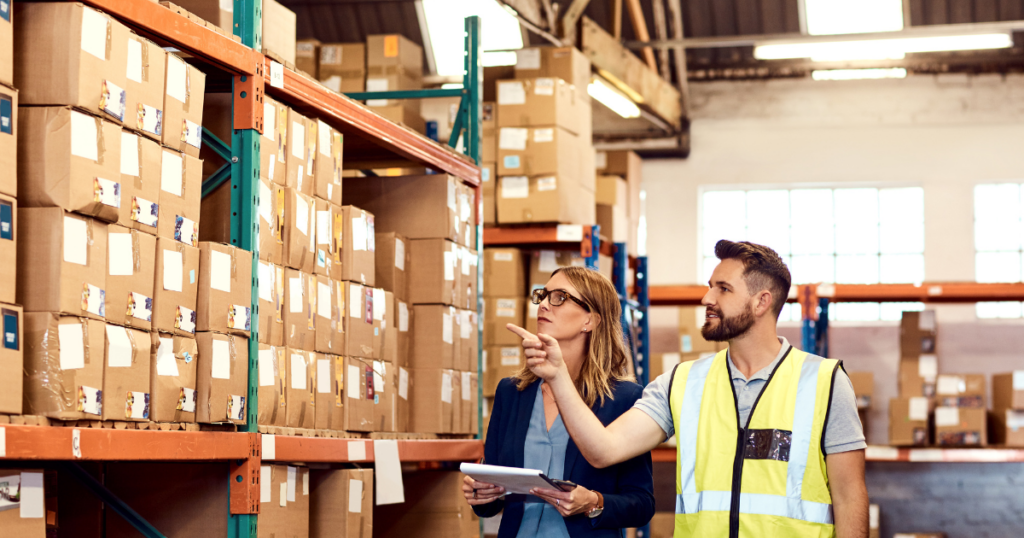
Understanding the Importance of Returns Management
Returns management refers to the process of handling and managing product returns from customers. It involves various activities such as receiving returned items, inspecting their condition, determining the appropriate disposition (resale, repair, or disposal), and updating inventory records accordingly. Effective returns management is crucial for several reasons:
- Customer Satisfaction: A seamless returns process enhances customer satisfaction by providing a hassle-free experience. Customers who have a positive return experience are more likely to become repeat buyers.
- Cost Reduction: Efficient returns management helps minimize costs associated with returned items. By quickly identifying resalable products, businesses can reduce inventory holding costs and avoid unnecessary write-offs.
- Inventory Optimization: Returns management allows businesses to gain insights into product quality issues, trends, and customer preferences. This information can be used to optimize inventory planning and procurement processes.
- Sustainability: Properly managing returns can contribute to sustainability efforts by reducing waste and promoting recycling or refurbishment of returned items.
Key Components of Effective Returns Management
To establish an effective returns management process in warehouse operations, businesses should focus on the following key components:
- Clear Returns Policy: A well-defined returns policy sets clear expectations for customers regarding return eligibility, timeframes, condition requirements, and refund or exchange options. It should be easily accessible on the company’s website or included in product packaging.
- Streamlined Return Authorization Process: Implementing a streamlined return authorization process ensures that all returns are properly authorized and documented. This helps prevent unauthorized returns and enables efficient tracking of returned items.
- Efficient Reverse Logistics: Reverse logistics refers to the process of moving returned items from the customer back to the warehouse or appropriate location. It involves transportation, sorting, inspection, and disposition activities. Implementing efficient reverse logistics processes minimizes handling time, reduces costs, and ensures accurate inventory management.
- Robust Inspection and Quality Control: Thorough inspection and quality control procedures are essential to determine the condition of returned items. This includes checking for damages, verifying completeness, and assessing whether the product can be resold or needs repair. Implementing automated inspection technologies can enhance accuracy and speed in this process.
- Effective Disposition Strategies: Based on the condition of returned items, businesses need to determine the appropriate disposition strategy. Resalable products can be reintroduced into inventory, while damaged or defective items may require repair, refurbishment, or disposal. Having clear guidelines and processes for each disposition option is crucial.
- Accurate Inventory Management: Returns management should seamlessly integrate with overall inventory management systems. Accurate tracking of returned items helps maintain inventory visibility, prevents stockouts or overstock situations, and enables timely decision-making.
- Continuous Improvement: Regularly analyzing returns data and customer feedback allows businesses to identify patterns, root causes of returns, and areas for improvement. By addressing these issues proactively, companies can reduce return rates and enhance customer satisfaction.
Best Practices for Effective Returns Management
To optimize returns management in warehouse operations, consider implementing the following best practices:
- Simplify Return Processes: Make it easy for customers to initiate returns by providing clear instructions and pre-paid return labels. Streamline the return authorization process to minimize customer effort.
- Automate Return Processing: Utilize technology solutions such as barcode scanning, RFID tagging, or automated inspection systems to expedite return processing and improve accuracy.
- Implement Data Analytics: Leverage data analytics tools to gain insights into return trends, product quality issues, and customer behavior. This information can guide decision-making and process improvements.
- Collaborate with Suppliers: Establish effective communication channels with suppliers to address product quality issues promptly. Collaborative efforts can help reduce returns caused by manufacturing defects or shipping errors.
- Optimize Packaging: Invest in packaging materials that protect products during transit and minimize the risk of damage. Consider using eco-friendly packaging options to align with sustainability goals.
- Train Staff: Provide comprehensive training to warehouse staff involved in returns management. This ensures they have the necessary skills and knowledge to handle returns efficiently and effectively.
- Monitor Key Performance Indicators (KPIs): Define and track KPIs related to returns management, such as return rates, processing time, disposition accuracy, and customer satisfaction. Regularly review these metrics to identify areas for improvement.
In conclusion, effective returns management is crucial for warehouse operations to enhance customer satisfaction, reduce costs, optimize inventory, and promote sustainability. By implementing clear policies, streamlining processes, leveraging technology, and continuously improving, businesses can establish a robust returns management system that contributes to overall operational success.