Automated Guided Vehicles (AGVs) in Warehouse Management: Revolutionizing Logistics
In the ever-evolving world of logistics and supply chain management, efficiency and precision are paramount. As businesses continue to grow and adapt to new technologies, the integration of Automated Guided Vehicles (AGVs) has emerged as a transformative solution. AGVs represent a significant innovation in warehouse management, offering a wide range of benefits such as increased efficiency, reduced labor costs, improved safety, and enhanced scalability.
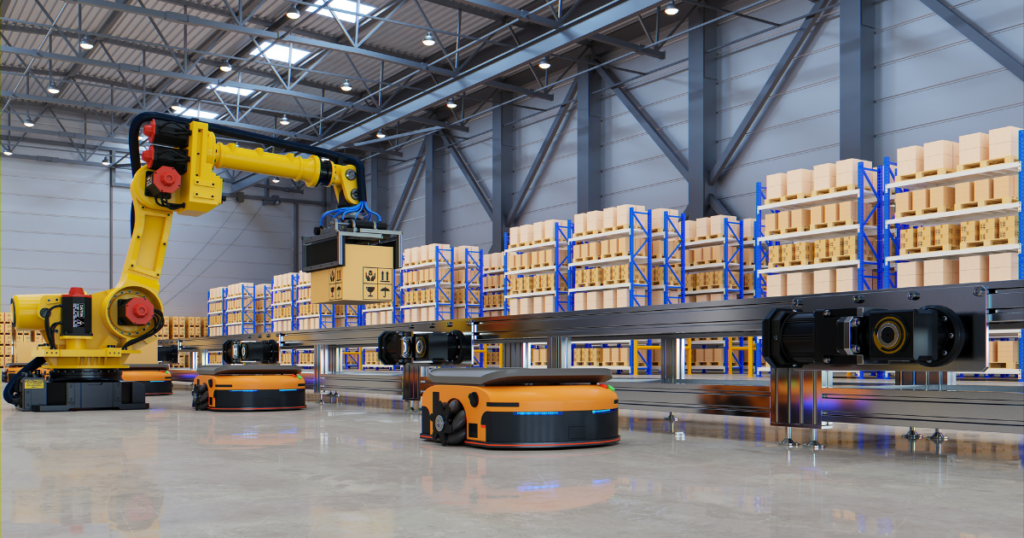
The Rise of AGVs: An Overview
Automated Guided Vehicles, commonly known as AGVs, are autonomous, computer-controlled vehicles that transport goods and materials within a controlled environment, typically warehouses, factories, or distribution centers. AGVs have become a game-changer in warehouse management, owing to their ability to navigate predefined paths, perform tasks without human intervention, and seamlessly integrate with existing warehouse systems.
AGVs were initially developed in the mid-20th century, primarily for manufacturing and material handling purposes. Over the years, their technology has evolved significantly, allowing them to cater to various industries and applications, including warehousing, e-commerce, automotive, pharmaceuticals, and more. The continuous advancements in sensor technology, artificial intelligence, and robotics have propelled AGVs into the forefront of modern warehouse management.
Types of AGVs
AGVs come in a variety of types, each designed to fulfill specific tasks and functions within a warehouse or manufacturing facility. The following are some common types of AGVs:
- Tow AGVs: Tow AGVs are designed to transport heavy loads by towing carts or trailers. They are widely used in manufacturing environments for moving raw materials, work-in-progress, or finished products within a facility.
- Unit Load AGVs: Unit Load AGVs are equipped to handle pallets, containers, or other unitized loads. They are commonly used in warehouses and distribution centers to transport goods from one location to another.
- Forklift AGVs: Forklift AGVs are designed to mimic the functionality of traditional forklifts. They can lift and stack pallets and other loads, making them suitable for tasks that require vertical movement of goods.
- Conveyor AGVs: Conveyor AGVs are equipped with conveyor belts or roller decks to move items along a continuous path. They are ideal for assembly lines and automated production processes.
- Automated Storage and Retrieval Systems (AS/RS) AGVs: AS/RS AGVs are specialized vehicles used in high-density storage systems. They work in tandem with automated storage and retrieval systems to efficiently manage and retrieve products from storage racks.
- Hybrid AGVs: Hybrid AGVs combine the capabilities of multiple AGV types, offering flexibility and adaptability to handle a wide range of tasks. They are highly versatile and can be customized to suit specific warehouse needs.
Applications of AGVs in Warehouse Management
The integration of AGVs into warehouse management has opened up a world of possibilities, streamlining various processes and enhancing overall operational efficiency. Some key applications of AGVs in warehouses include:
- Material Handling and Transportation: AGVs are extensively used for transporting goods from one location to another within a warehouse. They can efficiently move pallets, containers, and other materials, reducing the need for manual labor and minimizing the risk of product damage.
- Picking and Packing: AGVs equipped with robotic arms and grippers can be employed for order picking and packing tasks. They navigate through the warehouse to collect items and assemble them into orders, improving accuracy and speed.
- Inventory Management: AGVs play a crucial role in maintaining accurate inventory levels. They can autonomously conduct cycle counts and inventory audits, ensuring that stock levels are always up to date.
- Trailer Loading and Unloading: AGVs can be utilized to load and unload trailers, optimizing the loading process and reducing the time spent on these tasks. This is particularly valuable in distribution centers where rapid turnaround is essential.
- Cross-Docking: Cross-docking, the practice of unloading goods from incoming trucks and loading them directly onto outbound trucks with minimal storage time, is made more efficient with AGVs. They can swiftly transfer goods from receiving docks to shipping docks, reducing storage costs.
- Quality Control: AGVs equipped with sensors and cameras can perform quality control checks on products as they move through the warehouse, identifying defects and ensuring that only high-quality items are shipped.
Advantages of AGVs in Warehouse Management
The adoption of AGVs in warehouse management brings forth a multitude of advantages that have a profound impact on operational efficiency and competitiveness. Some key benefits include:
- Increased Efficiency: AGVs operate 24/7 without breaks, significantly increasing the speed and accuracy of material handling and transportation tasks. They can optimize routes to minimize travel time and reduce congestion in busy warehouses.
- Cost Savings: By automating repetitive and labor-intensive tasks, AGVs help reduce labor costs, including salaries, benefits, and training expenses. Additionally, they minimize the risk of accidents, which can result in costly workplace injuries and damage to goods.
- Improved Safety: AGVs are equipped with advanced safety features, such as obstacle detection sensors, emergency stop buttons, and collision avoidance systems. This ensures a safer working environment for both AGVs and human workers.
- Scalability: AGV systems can be easily scaled to accommodate changes in warehouse operations. Businesses can add more AGVs or reprogram existing ones to adapt to shifts in demand or warehouse layout.
- Enhanced Accuracy: AGVs are programmed to follow precise paths and instructions, reducing the likelihood of errors in material handling, picking, and packing processes. This results in higher order accuracy and customer satisfaction.
- Real-time Data and Analytics: AGVs generate valuable data regarding warehouse operations, such as vehicle performance, traffic patterns, and inventory levels. This data can be used to make informed decisions and optimize processes further.
Challenges and Considerations
While AGVs offer numerous advantages, their implementation does come with certain challenges and considerations:
- Initial Investment: The upfront cost of purchasing and implementing AGV systems can be significant. Businesses need to carefully assess their ROI and long-term benefits to justify the investment.
- Integration with Existing Systems: Integrating AGVs with existing warehouse management systems (WMS) and other automation technologies can be complex. Ensuring seamless communication and data exchange is crucial for maximizing efficiency.
- Maintenance and Repairs: AGVs require regular maintenance to ensure their proper functioning. Businesses must establish maintenance schedules and have backup plans in case of unexpected breakdowns.
- Workforce Transition: The introduction of AGVs may require a shift in the workforce. Businesses need to consider retraining employees for roles that complement AGV operations or offer opportunities for upskilling.
- Scalability Challenges: Scaling AGV systems to accommodate growth can be challenging. Expanding the fleet of AGVs or modifying their programming may require additional planning and resources.
The Future of AGVs in Warehouse Management
As technology continues to advance, the future of AGVs in warehouse management looks promising. Some key trends and developments to watch for include:
- Artificial Intelligence and Machine Learning: AGVs will become more intelligent through the incorporation of AI and machine learning algorithms. This will enable them to adapt to changing environments, make real-time decisions, and optimize routes more effectively.
- Enhanced Collaboration: AGVs will increasingly collaborate with human workers, robots, and other AGVs in a synchronized ecosystem. This will improve overall warehouse efficiency and flexibility.
- Autonomous Fleet Management: Fleet management systems will become more sophisticated, allowing warehouse managers to monitor and control large fleets of AGVs simultaneously. This will result in better resource allocation and task prioritization.
- Customization and Adaptability: AGV manufacturers will offer more customizable solutions to cater to specific industry needs and warehouse layouts. This will enhance their adaptability in various settings.
- Sustainability: There will be a growing emphasis on sustainable AGV technologies, including electric and hydrogen-powered AGVs. This aligns with the increasing global focus on reducing carbon emissions and environmental impact.
Automated Guided Vehicles (AGVs) have become a driving force in modern warehouse management, reshaping the way businesses operate and optimize their supply chains. CoreIMS, as a pioneer in the field of warehouse management solutions, has embraced AGV technology to empower businesses with a competitive edge.
The integration of AGVs into CoreIMS’s portfolio provides a holistic approach to warehouse management, with seamless integration, customization, real-time data insights, scalability, and adaptability. CoreIMS AGVs streamline material handling, picking, packing, inventory management, trailer loading, and quality control, offering businesses a wide array of benefits.